Case Studies
Customers

MH7 Precision find Redant to be a Superb Tool
MH7 Precision Engineering based in Brighouse, Yorkshire are finding significant benefits from the Redant Production Control System having purchased it from GB Efficiency Services.
The company was formed some 20 years ago as a “Toolroom” company providing tooling components such as chuck jaws and work holding devices for John Walton a local Tool Supply company. MH7 has grown over this period and now offers a range of Sub Contract machining services to a number of discerning customers including Borg Warner. As well as a selection of CNC Milling and Turning Centres MH7 also offer Gear Cutting and EDM services.
Business Owner Mark Hirst takes up the story. “Our previous system, like many small engineering enterprises, was very much paper based with a sprinkling of spread sheets and word documents. We used Sage for Accounts, but there was no link of data between the two areas. This resulted in poor visibility and control with numerous areas where data had to be duplicated risking input errors. In many instances due to lack of control despatches and invoices were not always accurately recorded resulting in un-invoiced work and lost revenue.”
“The first contact we had with Redant was via one of our suppliers who suddenly started to provide instant returns of accurate quotations. When I queried this, they said that they had installed Redant and were getting great benefits from its use. I therefore arranged for a demonstration from GB Efficiency Services the local dealer and found that it would be an ideal and cost-effective solution for us.”
Mark continues. “The system has now been installed for over 12 months and after 2 days training we were confident enough to start using parts of it straight away. With the day to day running of the system now being controlled by our Office Administrator my time is now dedicated to more important areas of the business.”
“We carry a significant number of customer component stock and this is now being entered onto the Redant Stock Control module so that we can instantly see what can be delivered from stock and what manufacturing orders need to be raised.
“The beauty of Redant is that you don’t need to implement all of it at once. We have so far just concentrated on the key areas for us and I am sure that we will expand into other areas as we find the need,”
“The main benefits we have gained from the system are as follows:”
- Quicker and more accurate Quotation turnaround
- Simple and speedy conversion of Quotes to Jobs Orders
- Simple and Comprehensive Traceability
- Integration to Sage (Including being able to work remotely)
- Tracking ALL despatches and invoices avoiding lost revenue
Mark concludes. “We have been very pleased with the training and support services whilst new updates and features are regularly available from the website at our request. From our experience, as we were recommended to Redant we can pass that recommendation on to any similar Precision Engineering company who are looking for a new system.”

Red Ant Production Control system increases productivity
Ackerman Engineering has seen an increase in shop floor productivity following the implementation of the Red Ant production control system.
Subcontract sheet metalworkers, Ackerman Engineering, undertook further expansion in 2006 when moving to new premises with a purpose-built 1600M industrial unit at Gore Cross Business Park, Bridport, providing the space and foundations for future growth.
As part of this expansion plan, a production control system was sought to replace the existing Dos system. The criteria when looking for a system was to find a comprehensive solution that would enhance efficiency and improve profitability.
The decision to invest in the Red Ant production control system was made following a number of meetings with director and programmer Mark Coleman.
'Red Ant was extremely comprehensive and we could see immediately that its implementation would be beneficial to us, however, nesting was one area we needed to address and was not at that time within the package,' said Graham Ackerman.
'Red Ant worked closely with us over a period of three months to develop a nesting module, which is now incorporated into the system.
'The nesting module has been a huge benefit within our organisation, allowing us to control and keep together all the small jobs without the labour-intensive bookwork,' he added.
Red Ant handles the manufacture and traceability of components supplied to blue chip companies such as Rolls-Royce, BAE Systems, Airbus, Aeroquip, Ifor Williams and Komatsu.
The system can: improve time management and cost control; maintain quality control to ISO, AS9100 and UKAS accreditation; keep detailed records and tailored analysis reports; improve time delivery; integrate with most accounts packages; and reduce stock levels.
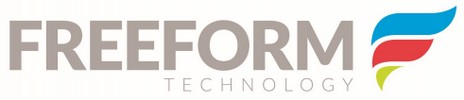
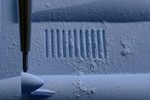
Freeform Technology Rev Up with Redant
F1 supplier Freeform Technology was established in 2008 by Fred Hutton and Simon Burchett to supply composite pattern and mould tooling. Having both worked at Red Bull Technology they saw a gap in the market for this type of work.
The first year was just Fred and Simon with one machine and over the years they have gradually built up their customer base, plant list and staffing levels. Freeform now have 18 employees and 5 - 5 axis CNC machines with key customers including Red Bull Technology, Mercedes GP, Lotus F1, Mclaren and numerous composite companies.
Alongside the F1 industry Freeform have moved into further areas including, Automotive, Medical and other non-F1 motorsport.
The current year turnover is predicted to be approx £1.6M.
Fred Hutton takes up the story, “On start up there was a need for a Production Control System and Redant was recommended by fellow F1 supplier – JK Engineering. After a demonstration Redant was proven to be user friendly and contained everything required to run a business of this type from quoting all the way through the production processes to invoicing and whilst also taking care of the time keeping of employees.
The system was implemented smoothly and quickly with excellent training and ongoing support and as there was no transfer of old data to worry about it made things easier.
Redant makes keeping track of customer deadlines very easy and keeps the possibility of a late delivery to an absolute minimum.
The inbuilt Drawing Register is very useful for remembering old jobs that have been through the system and can be found easily for re-quotation purposes.
We are delighted with the functionality and control that Redant has brought to our business enabling us to cope with the extra pressures as the business has expanded.
As we were recommended to Redant as a tried and tested system for manufacturing companies like ours we have also been happy to recommend Redant to others on many occasions”
Contact: Freeform Tech: Fred Hutton: 01280 820921
GB Efficiency Services: Graham Barran: 0113 274 7161. grahambarran@gbesl.com
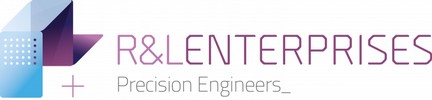
R & L Enterprises see Efficiency Gains with Redant
R & L Enterprises the Leeds based Precision Engineers and Laboratory Equipment Manufacturer have joined the ever-expanding list of Redant Software users having purchased the system from GB Efficiency Services.
The company was formed in 1942 and has been manufacturing & supplying laboratory metal ware worldwide since then. In recent years with major investment in modern CNC machine tools including sliding head & fixed head lathes along with machining centres the company manufactures sub-contract components & assemblies, which is now the major part of the business. Market sectors include fire suppression, telecoms and medical industries.
Technical Director Jonathan Bell takes up the story. “Our previous system was predominantly a stock control system that had been tailored to suit our needs over many years. It incorporated a very basic production control system and no real purchasing system. As a result, we spent a lot of time writing manual purchase orders and updating spread sheets on a daily basis which for a busy subcontract engineering company was very inefficient”.
“We spent 6 months looking at various production control systems on the market and after various demonstrations decided that Redant was the best system for us. The main reasons for choosing Redant being ease of use, value for money and integration of all the modules.”
Engineering Director Martyn Garner comments. “The system has now been installed for 18 months and after 3 days training we were confident enough to start using parts of it straight away. In fact our customers were amazed at the instant turnaround in quotes that was now being achieved.”
“Due to the large number of parts and assemblies we produce both in the laboratory and sub contract markets, we spent 3 months inputting and updating all the data from our old system whilst trialling Redant and went fully live at the beginning of 2012”.
“The main benefits we have gained from the system are as follows:”
- Reduced Lead Times
- Reduced Stock Holding
- Reduced Work In Progress
- Improved Customer Service Levels
- Improved Quality Control
- Better and Easier adherence to ISO 9001
- Quicker and more accurate Quotation turnaround
- Simple and speedy conversion of Quotes to Jobs Orders
- Simple and Comprehensive Traceability
- Accurate Job Scheduling to customer requirements
- Scope of reports that can be generated
Jonathan Bell concludes. “We are in the process of implementing Data Collection and are likely to implement the Finite Scheduling module in the future”.
“We have been very pleased with the training and support services whilst new updates and features are regularly available from the website at our request. From our experience we can fully recommend Redant to any similar Precision Engineering companies”.
Contact: R & L Enterprises. Jonathan Bell. 0113 395 5208.
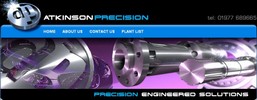
Atkinson Precision “Strike Oil” with Redant Software
Atkinson Precision the Leeds based Precision Engineers and suppliers to major Oil Field Industry customers have gained significant benefits since their investment in the Redant Production Control System.
Contracts Manager Guy Bradstock evaluated the systems market and chose Redant for its wealth of rich functionality covering all areas of the business and its cost-effective pricing.
The Redant system provides a fully integrated solution fulfilling all of their needs from initial Enquiry right through to Invoicing and integration to the accounts ledger. In particular Oil Field Customers require stringent Quality Control and Traceability which is more than adequately met with the extensive functionality inbuilt in Redant such as Contract Review, Concessions, Non-Conformance Procedures, Equipment Calibration, Inspection Procedures and Full Lot Traceability.
Guy is presently transferring the due dates generated in the Redant Finite Scheduler to create Customer Based Delivery Schedules in MS Project which the customers find to be most useful. This is now being considered as a system enhancement to provide an automated transfer from Redant to MS Project.
Amongst the many time saving and efficiency features in the system Guy finds the integrated emailing facility with drawing attachments and the ability to scan and attach documents to Jobs and Parts particularly beneficial.
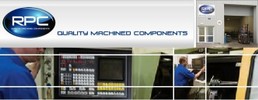
Roles Precision achieve ISO9001 with Redant Software
Roles Precision the Cramlington, Northumberland based Precision Engineers and supplier to Komatsu and Caterpillar continue to gain benefits from their investment in the Redant Production Control System.
Mark Jenkins the Managing Director evaluated the systems market and chose Redant for its wealth of rich functionality covering all areas of the business and its cost-effective pricing.
The Redant system carries numerous threads of Quality Control functionality such as Contract Review, Concessions, Non-Conformance Procedures and Reporting, Equipment Calibration, Inspection Procedures and Full Lot Traceability. These functions have helped Roles to achieve the ISO 9001 Accreditation which was essential for the Quality Standards demanded by their high-profile customers.
Now that the basic system modules have been implemented and the benefits are flowing the next stage is to be commenced. This will consist of the Finite Scheduling and Shop Floor Data Collection modules.
The integrated Touch Screen Data Collection and Time and Attendance System will provide a dual function for Time and Attendance recording and basic HR records of all employees and a Real Time Job Time Recording System on the shop floor. However, the Redant Data Collection System goes further than just collecting Labour Bookings. In essence it is a Manufacturing Execution System (MES) providing shop floor supervisors and operatives with views of Work Schedules, Jobs, Routes and even Drawings.
The Finite Scheduling Module which will benefit from receiving timely and accurate Job Bookings will then provide Roles with a flexible “Visual Planning Board” where various What if? Scenarios can be played out to enable the optimum planning schedule to be determined within the finite resources available.